The Black Magic of Consumables Transfer
David Keen, Director of Pharmaceutical Microbiology for Ecolab Life Sciences, shares his observations and best practices for cleanroom transfer disinfection.
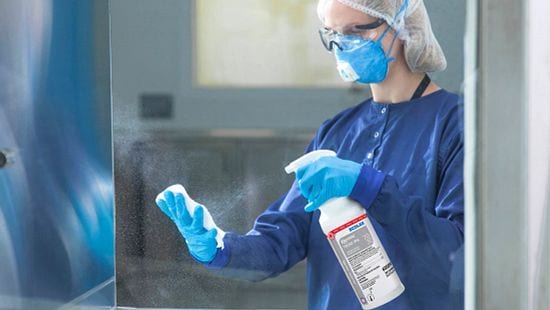
Until I joined Ecolab I had absolutely no idea that there was a link between Harry Potter, Tinker Bell, Gandalf and some pharmaceutical manufacturers. What is the link? Magic of course.
Where and why are pharmaceutical companies utilizing the dark arts (and I am not talking about Microbiology – I can hear all of you Chemists out there…). It is in the science of transfer disinfection. I have seen a number of truly eye‐opening practices in the industry that lead me to conclude that in the absence of anything resembling a structured approach to transfer disinfection, the company must be relying on hope or magic. The magic I am talking about is a powerful one, it allows dirty items from external environments to be brought into cleanrooms with no transfer disinfection. Any contamination that is present on the items, whether microbial, chemical, or physical are apparently prevented from leaving the transfer area by magic alone.
Here are three examples I have witnessed in the last 12 months.
- A company brought in a pallet of finished product consumables from an external warehouse. The pallet and outer wrap were visibly black with physical debris. The pallet and the consumables on it were pushed into a Grade C transfer airlock (there was no Grade D area between the two areas). The doors were closed, and the items were then wheeled into a Work in progress (WIP) store for immediate use. At no point were the contents transferred onto another (clean or captive) pallet, the dusty outer wrap removed, or a chemical disinfectant of any type applied. When I queried their environmental monitoring results for the transfer airlock, they did not perform any. However, they were perplexed at the high level of spore forming bacteria they routinely recovered in their Grade C cleanrooms.
- A second company only used alcohol spray in the transfer of items into its cleanrooms, regardless of where those materials came from. Again, when we looked at their environmental monitoring data, we found atypically high levels of bacterial spore formers in those areas. As in the previous example, the company had an open, long term investigation into where they could be coming from. Lack of use of a sporicidal disinfectant for transfer disinfection was not on their imminent CAPA list.
- The final example even has a catch phrase associated with it which some will be familiar with – ‘Spray and Pray’. Here items were added into a transfer hatch and then a trigger spray of disinfectant was used a random number of times in the general direction of the items added to the hatch, against the flow of air created by the pressure cascade. No wiping of the items was performed and certainly no disinfectant contacted those surfaces of the items that were in direct contact with the base of the transfer hatch. In this instance there is a slight twist to the narrative as environmental monitoring was performed in the hatch, but only on those surfaces that had seen some spray (and subsequent prayers). The satisfactory data from the sprayed surfaces was unsurprisingly at odds with the data from the cleanroom area in the vicinity of the hatch. How did all three different reputable companies manage to get it wrong? And, indeed, had they got it wrong?
Ecolab does not have a school of magic education, so I can only comment on best practice for mortals.
The most commonly used disinfectant for transfer disinfection is traditionally alcohol. It is a great choice, as it if fast acting, has a broad spectrum of activity against vegetative cells and leaves little or no chemical residue behind. It comes in a myriad of formats from reputable suppliers to fulfill the needs of most aspects of transfer disinfection. Its one major drawback? It is not sporicidal. Spore forming bacteria and mold spores normally come under the general heading of ‘environmental isolates’ when they are recovered from a cleanroom. These organisms are naturally present in the outside world and can be found in particularly high numbers in soil, wood, and man‐made materials such as cardboard.
One route of ingress for these types of microorganisms into a cleanroom is by their presence in high numbers on these ‘high risk’ materials such as wooden pallets and cardboard boxes. Then subsequently ‘hitching a lift’ on consumables that have been in contact with these materials that are then destined for cleanroom areas. For this reason, elimination of wood or cardboard, ‘de‐trashing’ or removal of outer wrapping is required at appropriate points. As is the need for a sporicidal disinfectant at some point in your transfer process from the warehouse to product contact areas, preferably at the beginning of the process, where the bioburden level is likely to be higher. The requirement to consider sporicides for transfer disinfection rather than alcohol alone is not a new one.
The PIC/S Recommendation on the Validation of Aseptic Processes PI 007‐6 January 2011 states:
“Sporicidal agents should be used wherever possible but particularly for “spraying‐in” components and equipment in aseptic areas.”
The MHRA Guidance for Specials Manufacturers 2015 states:
“Before transfer to the manufacturing room, a sanitization step using a spray and wipe technique including a sporicidal agent designed to inactivate bacterial and fungal spores must be carried out.”
FDA Aseptic Processing Guide states:
“It is critical to adequately control material (e.g., in‐process supplies, equipment, utensils) as it transfers from lesser to higher classified clean areas to prevent the influx of contaminants. For example, written procedures should address how materials are to be introduced into the aseptic processing room to ensure that room conditions remain uncompromised. In this regard, materials should be disinfected according to appropriate procedures…”
Annex 1 Feb 2020 v.12 DRAFT REVISION 4.12 ii states:
- “Pass‐through hatches should be designed to protect the higher grade environment, for example by effective flushing with an active filtered air supply.
- The movement of material or equipment from lower grade or unclassified area to higher grade clean areas should be subject to cleaning and disinfection commensurate with the risk and in line with the CCS.”
Heavily soiled outer wrappers should be removed first and discarded. The same applies for dirty pallets. ‘Captive’ pallets (pallets manufactured from a more suitable material such as metal or plastic, that are subject to regular documented cleaning and disinfection, and that remain, or are ‘captive’ in a specific cleanroom grade) can be useful. Items to be disinfected as part of material transfer should be wiped with the disinfectant as mechanical action greatly increases the efficacy of a disinfection process and allows greater contact of the disinfectant with the microbes. The mechanical action of the wipe will also remove some of those organisms that the disinfectant cannot kill, such as endospores.
So, if you work in a Life Sciences site, you cannot find Tinkerbell, Harry Potter is back at school and Gandalf is in the Bahamas, consider the following:
- Consider a sporicidal disinfectant to be used in partnership with alcohols at some point in your transfer process.
- Always spray and wipe ‐ spraying on its own is not good enough.
- Ensure surfaces presented for disinfection are clean and free from physical debris. Remove outer wrappers, change pallets and eliminate or discard cardboard.
- Ensure your environmental monitoring program covers the transfer process.