How Digital Solutions Can Become the Best Ally for Food Safety Compliance
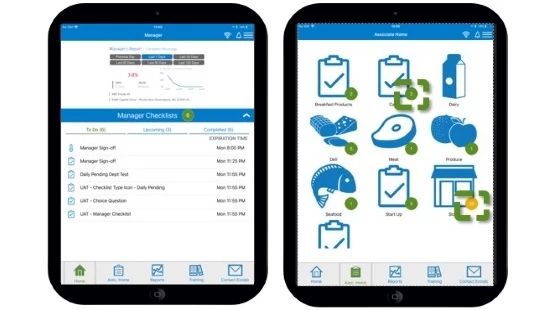
Nowadays, food service operations encounter an overwhelming list of regulation and compliance requirements that could become a real challenge to meet fully.
Many operational requirements can divert energy, focus and resources away from the core of the business—providing safe, high-quality food in a cost-effective manner.
As many other industries have experienced, the key to controlling and managing such possible distractions is technology and automation.
Let’s look at a couple of examples related to everyday food service operations and how using the correct technology tool can result in giant leaps forward in efficiency, control and traceability.
1. Printed checklists
For decades, almost every food retail store, restaurant, or catering service has used printed food safety checklists to track the execution and monitoring of cleaning and sanitation Standard Operating Procedures (SOPs), control cooking time and temperature for high safety risk foods, and even to register certain aesthetic aspects of the site such as restroom and main hall floor cleaning frequency.
Although in principle, carrying out these controls is commendable, in reality, traceability, transparency, and above all, timely detection of critical deviations, are lost among the hundreds of printed checklists that are manually filled out every day and piled up in folders and boxes month after month, year after year.
Could anyone find precise data or a negative trend that needs to be corrected among so much paperwork? Most probably not. Additionally, from an improvement perspective, the whole purpose of filling hundreds of forms and checklists every month is to have them in case of a visit from an authority, rather than to make the operation more efficient, simplify processes or prevent systematic deviations.
2. Training new employees
In any organization there will always be staff turnover. The addition of new talent is something constant in the operation and in many cases, the cause behind inconsistencies in the execution of critical SOPs that lead to high risks in safety, regulatory compliance and the brand's quality standards.
Imagine if a new employee, who did not have the opportunity to be adequately trained or their induction process was insufficient, forgets the correct and safe temperature for cooking the store’s chicken, or does not know at what temperature it should be stored.
Now suppose that chicken is the best seller in the store and dozens of consumers become ill from food poisoning due to mishandling. It is not difficult to imagine the great damage to the reputation of the store's brand and how this could impact sales and profitability. It goes without saying that in today’s social media times, such negative incidents can become even more explosive, further prolonging the damage in consumers’ minds.
In both examples, the common denominator is the lack of digital technology and not leveraging its unlimited advantages to make more efficient the mechanisms of execution, verification and measurement.
In response to these and many other related challenges, Ecolab developed MARKETGUARD™ 365—a digital solution that enables documentation and consistent paperless control to help increase compliance in the most relevant daily aspects of food service operations, accomplish precision in data collection, and significantly improve operational performance.
MARKETGUARD ™ 365 consists of a powerful duo of an App for mobile devices and a
Web portal with a platform that can be fully customized for the cleaning and
hygiene processes, checklists and food safety protocols of each operation. It is an easy and simple training tool that ensures the correct execution of critical controls by new employees from the start, while minimizing omissions that can happen due to employees’ lack of knowledge.
From a managerial standpoint, MARKETGUARD ™ 365 becomes their best ally to easily manage, measure and comply with today’s food service operational requirements, without paperwork headaches.
Today's market demands transparency, efficiency and consistency in compliance with controls for each shift—exactly what brands need to keep their quality promises to their consumers.