ACTRENE™ ANTIFOULANT SAVES MILLIONS OF DOLLARS IN ETHYLENE PRODUCTION
THE SITUATION
One of the most common and costly issues faced in ethylene plants is fouling in the light ends fractionation area. The results of unwanted polymerization span from the costs of swapping and cleaning reboilers to reduced throughput and ultimately unit shutdowns. A North American ethylene plant was experiencing fouling in the depropanizer tower on a regular basis. This fouling caused throughput restrictions that required turnarounds for cleaning every 2.5-3 years.
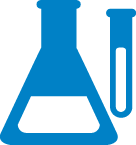
THE SOLUTION
Nalco Water surveyed the system using a total system problem-solving approach from a mechanical, operational and chemical (MOC) standpoint. A team of subject matter experts from Nalco Water and the customer was formed, and a combination of laboratory testing, computer modeling, and the use of our proprietary Light Ends Fouling Model were employed.
Using the knowledge gained from the comprehensive system survey, we worked with the customer to develop and implement a new ACTRENE™ antifoulant program on the depropanizer tower.
The safer, more reliable operation saved the customer millions of dollars in lost production, maintenance, cleaning, and turnaround costs.
THE RESULTS
Implementing a new ACTRENE antifoulant program on the depropanizer tower:
- Greatly reduced depropanizer fouling
- Tower runlength dramatically increased
- Tower was exceptionally clean when inspected
- Improved depropanizer reboiler performance
As a result of the comprehensive problem-solving approach fouling in the depropanizer tower and reboilers was greatly reduced; eliminating the light ends fractionation area as a throughput limitation and allowed the customer to operate on a scheduled turnaround basis.
Related Stories
Visitors who viewed this story also viewed