
Leading International Brewer in Africa Improves Efficiency and Productivity with Ecolab’s 3D TRASAR™ Pastoskid, Saving $27,600 Per Year
Total Value Delivered: $27,600K Annually and 288 Hours of Additional Production Time
Background
A leading international brewing company in the African beverage market is committed to advancing their sustainable development approach and meeting the expectations of its stakeholders. One of their breweries, located in the eastern part of Democratic Republic of Congo, has an annual production capacity of 1.8 million hectoliters and has shown opportunities to contribute to the company’s sustainability goals.
One of the major issues the brewery was facing was a high bottle breakage rate of greater than 0.1% in two of the pasteurization machines. A high bottle breakage rate enables the growth of nutrients at the ambient temperature of less than 60 degrees Celsius. These conditions can cause substantial microorganism growth, which in turn had several negative implications:
- Blockage in the filter screen and sieve plate resulted in uneven water distribution leading to dynamic water imbalance and higher water consumption.
- Due to heavy blockage in the filter barrels and screen, a team member had to spend 4 hours cleaning the filter barrels and screen per day before normal production could resume.
This impacted the brewery’s overall uptime and productivity.
- Uneven heating from heavy filter blockage had the potential to impact the beer’s taste and quality.
- Moreover, the manual dosing of biocide chemicals gave off a strong pungent smell, which negatively impacted the health and safety of brewery employees.
Solution
After an in-depth on-site survey and data analysis, the Nalco Water team suggested implementing the 3D TRASAR™ PASTOSKID Technology. This technology effectively controls microbial fouling, provides greater control of the tendency for metal corrosion and significantly improves operational reliability. It also ensures the active balance of biocide, corrosion inhibitor and the critical water parameters for the whole water system. The Nalco Water team showed the customer how implementing this technology would result in significant operational cost savings, as well as reduce the brewery’s environmental impact.
Nalco Water’s 3DT TRASAR™ PASTOSKID Technology includes:
- Oxidant Controller (NOC) – Enables real-time, online monitoring of the water channel, accurately measuring and optimizing the dosage of oxidizing biocide and maintaining the proper low temperature. The system also has self cleaning sensor technology, allowing better control the microbial fouling in pasteurizers.
- Nalco Water’s patented 3D TRASAR™ technology – Controls the dosing of oxidizing biocide at the high-temperature zone to ensure accurate and optimized chemical dosage. The technology can prevent the product from remaining too long in the high-temperature zone, and thus avoid product packaging corrosion.
- Brominator – This technology reduces the frequency of manual feeding for chemicals. Solid chemistry also avoids the potential risk of chemical volatilization which can harm the human body. It is well packaged and occupies very little space.


Photo left: Uniform spray through clear spray nozzles. Photo right: Nalco Water oxygen controller.
Results
Because of the real-time automation technology implemented at this brewery, the plant was able to save 3 million liters of water and 500,000 megajoules of energy annually, which resulted in $27,600 in cost savings. The microbial fouling issue was controlled at the ideal low-temperature zone in the pasteurizer. With online NOC monitoring, PASTOSKID technology could control the free Bromine within the favorable range of 2 to 5 ppm, so that the screen and barrel of the water tank in the system were less polluted by the microbial film. The whole water system had a good dynamic balance of flow rates and uniformity of water temperature across different temperature zones.
Unique benefits of Nalco Water’s solution:
- Increased Safety – Online monitoring capabilities reduces the chance of exposure to harmful gases generated from regular treatment chemistry. Also, safety risks caused by chemical leaks and sprinkling during the liquid chemical dosing are reduced.
- Easy Handling – The amount of labor hours needed to monitor the chemicals are reduced.
- Improved Performance – The solid chemicals help to maintain the correct water temperature. This improves performance and stability of microbial control in the pasteurizer water system.
- Sustainability – The program reduces water and energy consumption along with reduction in use of chemicals and auxiliary equipment such as pumps and chemical barrels, allowing for better use of space.


Photo left: 3D TRASAR™ PASTOSKID unit with controller at customer site. Photo right: Brominator
Conclusion
Ecolab’s 3D TRASAR™ PASTOSKID Technology has helped this brewery overcome some of their biggest obstacles. Overall, the program helped them to solve the microbial fouling issue, eliminate food and operator health safety risks, improve operational efficiency, save water and energy, and reduce the total cost of operation.
Following this success, the beverage production company is endorsing Nalco Water’s technology across its subsidiaries and has already begun to implement the technology in more facilities.
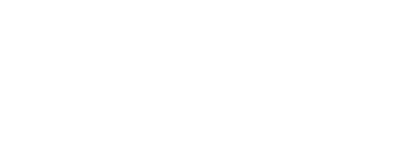
Annual Savings*
-
Water
3 Million LitersWater Savings Per Year
-
Productivity
288 Hours*Additional Production Time Saved Annually
-
Energy
500,000 MJ*Energy Savings Per Year
-
Reduced Freshwater Use By
$27,600 Annually
*Client Supplied Data