
Semiconductor Fab Saves Water, Cost and Environmental Impact via Improved Visibility into Process Cooling Water (PCW) Operation
Background
A large U.S.-based semiconductor fab was experiencing a variety of operational challenges in their process cooling water (PCW) loops, which negatively impacted the site in several ways:
CHALLENGE |
RESULT |
IMPACT |
Undetected water leaks |
|
|
Insufficient visibility to PCW conditions |
|
|
Uncontrolled water discharge |
|
|
The fab’s utility managers suspected several of these issues but lacked the compelling data to diagnose and quantify the impact of the problems. This made it difficult for the fab to prioritize troubleshooting and corrective action.
Solution
The fab implemented a Nalco Water treatment program to help manage its PCW system. To manage water quality within the PCW loops, a 3D TRASAR™ program was introduced with the following capabilities:
- Inert tracer to monitor water losses, which are common in PCW systems
- Real-time corrosion measurement to affirm corrosion control performance
- Real-time pH and conductivity measurement to detect process in-leakage
Soon after start-up, data from the 3D TRASAR controller revealed, for the first time, water leaks occurring in the PCW loops.
Based on the decay rate of the inert tracer over a specific period of time and the known volume of the loops, a precise calculation of water loss was possible. Prior to this, the only indication of water loss was the position on the make-up water valve to the loops.
Next, the fab’s utility management team and tool owners were equipped with resources to identify where leaks were occurring so tool owners could take appropriate remedial action. The following approach was taken:
- Additional specialized fluorescent tracer was added to PCW loops, measured at a different wavelength to distinguish from treatment chemistry.
- Tool owners were provided with fluorometric pens to check each floor drain. This test was designed to be fast, simple and reliable, enabling quick detection without requiring in-depth knowledge by the operator.
- If tracer was detected, the facilities team and tool owner were notified. In most cases, leaks were promptly resolved. Detection of the tracer at the drain of a tool cluster enabled specific clusters to be the focus of additional investigation. Heat exchangers associated with that tool cluster were checked, including pressure testing and exchanger replacement when needed.
The inert tracer in this application was chosen for several specific characteristics:
TRACER FEATURE |
BENEFIT FOR LEAK DETECTION APPLICATION |
Functions at a different spectrum than those used in the PCW loop’s treatment chemistry |
Distinct measurement without interfering with the PCW loop treatment program |
Response is independent of pH and temperature |
No specialized conditions required for measurement; broad applicability |
Response is in a very low background region of the spectrum |
Provides visibility in a region of the spectrum where other potential interferents would be rare |
Response is strong at low concentration |
A little goes a long way: detection is a simple yes/no condition |
Rapid, accurate and easy to use |
Tracer pen does not require advanced operator skill |
Results
This work yielded several significant improvements for the fab:
Reducing water leaks from the PCW loops saved an estimated 10.9 million gallons of water per year.
Azole levels in the fab’s effluent were reduced by 64% — a decrease of 7,260 lbs. This eased the local publicly owned treatment works’ (POTW) concern regarding incoming azole concentrations.
The program stabilized chemistry within the fab’s PCW system, which reduced their corrosion risk and cut demand for hands-on operational attention. As a result, staff and vendor labor resources could be reallocated to higher value tasks.
The combination of reduced chemical spend and UPW operational cost generated net savings of more than $674,000 per year. This team effort also provided the fab with an internal framework to maintain the gains going forward.
_
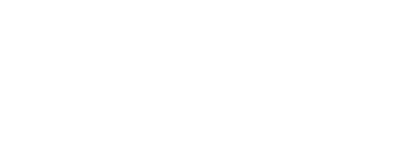
Annual Savings
-
Water
10.9 million gallons*(41.3 million liters) per year
-
Cost
USD $674,000*per year
-
Environmental Responsibility
64% per year*Reduced azole discharge
-
Total Value Delivered:
USD $674,000 annually
*Client Supplied Data